

Supply-chain stability considerations are being prioritized by various automotive OEMs and cell producers who are looking to secure local (recycled) raw material volumes at stable prices. 2 “European Battery Alliance,” European Commission, October 2017 “Programs for small businesses," National Science Foundation.
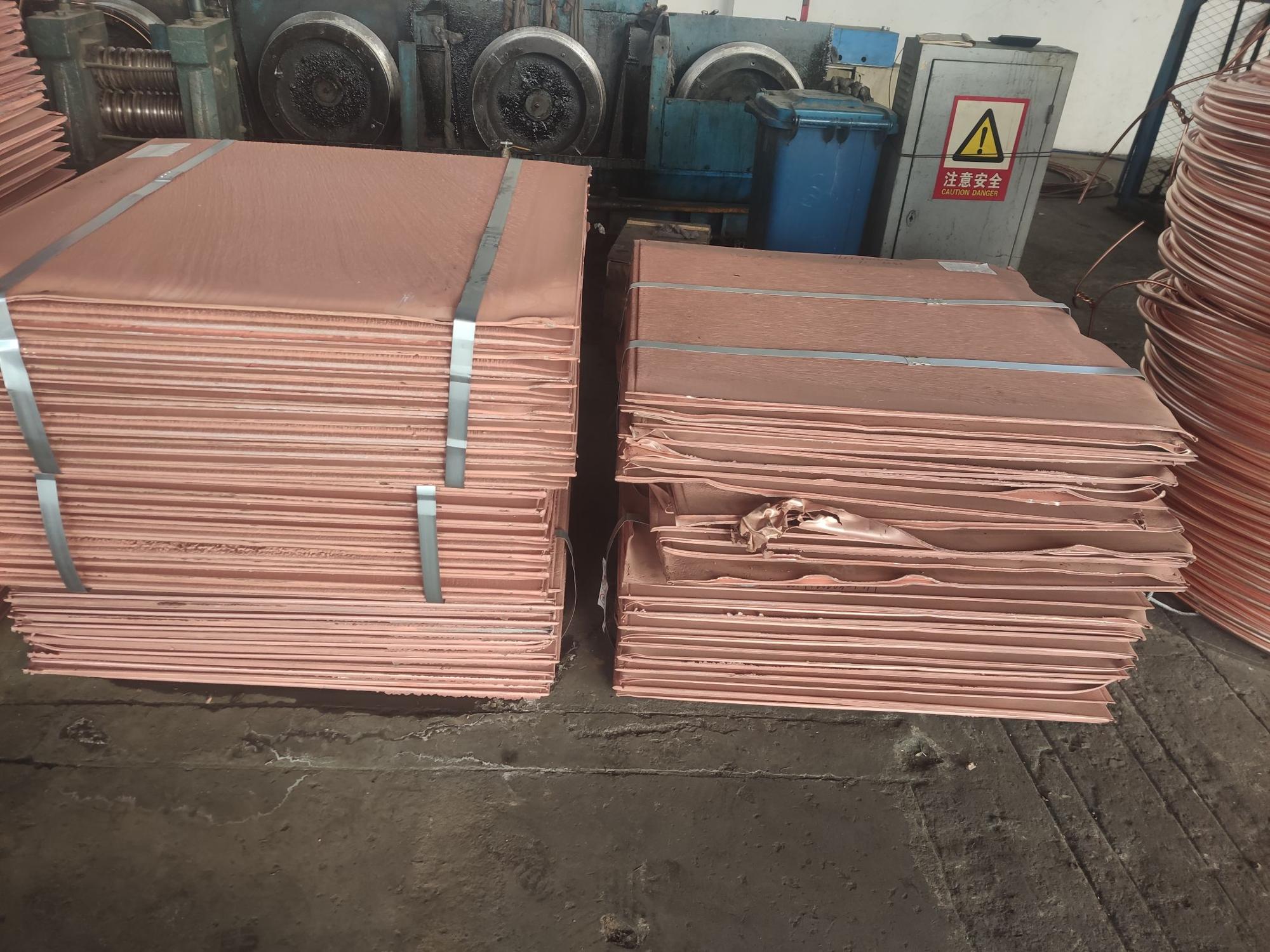
In addition, research and innovation project grants from governments are promoting recycling technology advancement, such as the EU’s European Battery Alliance and the United States’ National Science Foundation Phase II Small Business Innovation Research grants. Technological progress as processes scale and mature is enabling higher recovery rates, lowering greenhouse-gas footprints, and improving economics. Numerous levers are fueling growth in the battery-recycling industry: While our research is tightly focused on battery recycling, we find that understanding the potential scope of the circular economy for batteries sheds light on a supply chain approach that could be adopted by other industries, within and beyond energy and transportation, to drive sustainable growth. In this article, we examine the market context that has led to growth in battery recycling, common technology pathways and business models, and success factors in this sector. This is especially the case for batteries using chemistries based on high-value inputs (for example, nickel-manganese-cobalt oxide cathodes) in comparison to chemistries with low-value inputs (such as lithium-iron-phosphate cathodes), though commodity fly-ups, geopolitical shocks, and regulation have the potential to shift the recycling business case, even for nickel and cobalt-free batteries. Batteries that are suitable for these second-life applications may well take this detour on their way to being recycled but, when taking a value-maximizing approach, all EV batteries should eventually find their way into recycling processes. Upon reaching their end-of-life in EVs (typically after ten to 15 years or more than 200,000 miles), EV batteries can find profitable second-life applications, such as stationary backup power, among others, which have less rigorous cycling demands than EVs. This can create an additional revenue stream for battery owners before those batteries are recycled. Unlike consumer electronics batteries, which are too small to integrate into second-life systems, and cell production scrap, which cannot be used in batteries, end-of-life EV batteries can be profitably remanufactured and used again in other applications. Yet, globally, production scrap will likely remain the primary source of battery materials for recycling until 2030, when end-of-life EV battery volumes will have grown to the point of overtaking (Exhibit 1). In markets where EV adoption has been pervasive for some time, such as China, end-of-life EV batteries represent a greater volume. With cell manufacturing scrap being as high as 30 percent when a new battery factory launches, a significant source of volume for recycling evolves in markets where EV battery manufacturing is kicking into high gear. In China, Europe, and the United States, which are all undergoing a large EV transition, most of the battery material suitable for recycling still comes from consumer electronics cells, such as those in laptops and other household items, and cell manufacturing scrap generated from faulty batteries that don’t pass quality control. This article is a collaborative effort by Andreas Breiter, Martin Linder, Thomas Schuldt, Giulia Siccardo, and Nikola Vekić representing views from McKinsey's Advanced Industries Practice. Battery recycling is the key to pursuing that opportunity (see sidebar, “Batteries’ second lives: An additional revenue stream”).
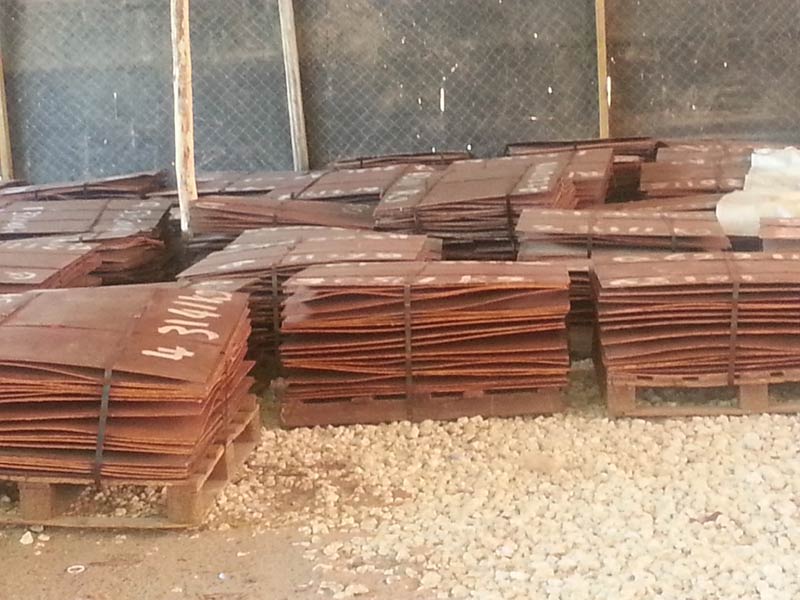
With this challenge comes an opportunity-to scale a supply chain that is more stable, more resilient, more efficient, and more sustainable than that of the fossil-fuel and internal combustion engine (ICE) vehicle industry. Moving from fossil-fuel based to electric mobility is a clear positive for the environment and for many consumers’ pocketbooks, but overhauling our transportation system requires new supply chains to be designed and scaled.
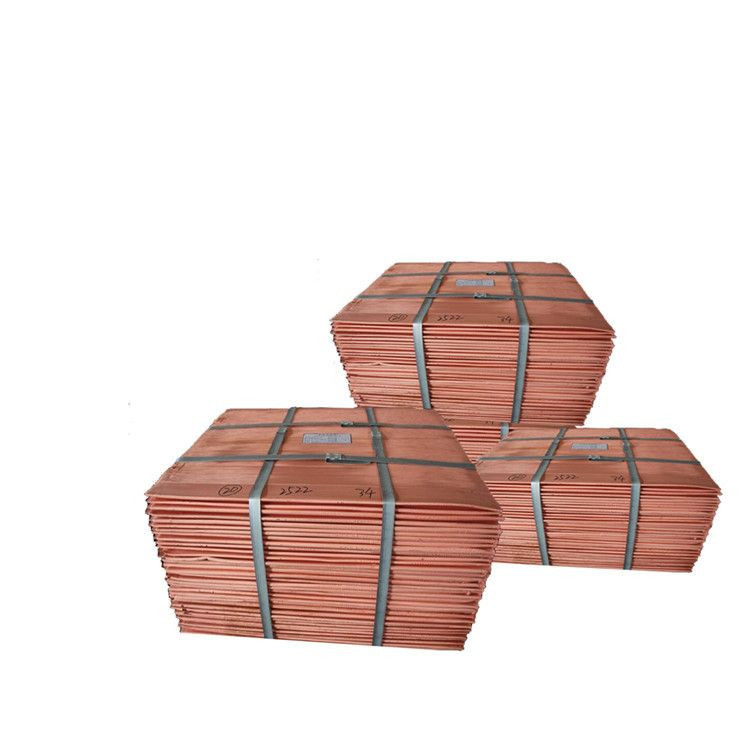
There is also considerable growth in EV battery volumes as they approach end-of-life, with over 100 million vehicle batteries expected to be retired in the next decade. This demand has led to considerable growth in battery production, with over five terawatt hours (TWh) per year of gigafactory capacity expected globally by 2030. As electric mobility increases globally, so does the need for electric-vehicle (EV) batteries.
